plastic box mold video
3 year ago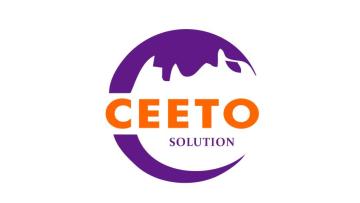
Plastic boxes, also known as logistics boxes, are widely used in industries such as machinery, automobiles, home appliances, light industry, electronics, etc. They are acid and alkali resistant, oil resistant, non-toxic and odorless, and can be used to hold food. They are easy to clean, have convenient parts turnover, neatly stacked, and easy to manage.
Mainly made of food grade environmentally friendly LLDPE material, it is refined through the world's most advanced rotary molding process and is equipped with marine stainless steel lock catch. The bottom is equipped with rubber anti slip pad, which is non-toxic, odorless, UV resistant, and not easy to change color. The surface is smooth, easy to clean, has good insulation effect, is not afraid of falling or touching, and can be used for a lifetime. The product is used in conjunction with an ice bag, and its cold insulation effect exceeds the same industry standard in the United States. Continuous refrigeration and insulation time can reach several days.
Daily commodity injection mould are tools used to make a variety of plastic products, including disposable cups. The process of producing disposable cups involves several key steps:
1. ** Design and make molds ** : First of all, we need to design molds according to the design requirements of the cup. The mold usually consists of two parts: the moving die (the part that moves with the injection molding machine) and the fixed die (the fixed part). The shape inside the mold determines the shape of the final product.
2. ** Select materials ** : The production of disposable cups is usually used in polypropylene (PP), polyethylene (PE) and other food grade plastic materials. These materials have good transparency, heat resistance and safety.
3. ** Injection molding ** : In the injection molding machine, the heated melted plastic is injected into the mold through high pressure, and the desired cup shape is formed after cooling. This process requires precise control of temperature, pressure and time to ensure product quality and consistency.
4. ** Stripping and dressing ** : The cup after forming needs to be removed from the mold. For some complex designs, manual or automated equipment may be required to complete the demoulding process. After taking out the product, it also needs to carry out the necessary finishing work, such as removing the raw edge.
5. ** Quality inspection ** : The final step is to conduct a quality inspection of the finished products to ensure that they meet the specifications and are free of defects.
Similar Video Recommendation
You May Also Like
If you are interested in the product, contact Bossgoovideo.com for more information
- *To:
- Zhejiang Ceeto Mold Co.,Ltd.
- *Message:
-
Submit
Main Product:
Plastic Injection Mold,
Plastic Molding,
Daily consumer plastic molds ,
automotive plastic molds,
lighting cover plastic molds,
home appliance plastic molds
You May Also Like