Electrocoaggulation Test 2
2 year ago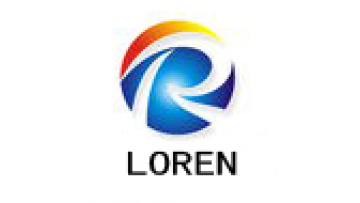
Feature & Outstanding Characteristic
-Adapt to a Wide Range of Wastewater to Handle a Variety of Pollutants
-30-Year Applied Unique Special Electrodes Layout with No Blocking
-Electrodes Last for 100 to 250 days as per different Site Condition
-Low Investment Costs with High Volume Throughut
-Low Operating Costs
-Low Maintenance and Repair Costs
-No Need to add Any Chemicals
-Small Footprint
-Simple Operation and High Degree Of Automation
-Short Processing Time and High Processing Efficiency
-Equipment Processing Produces Less Sludge And Sludge
-Fast Purification Speed
-Easy Operation
- Convenient Maintenance
Definition
Electrocoaggulation or Electroflocculation Process Belong To Electrical Chemistry Technology, which Can Be Used Alone Or In Combination With Other Treatment Methods To Rapidly Improve The Biodegradability Of Industrial Wastewater Such As Refractory Organic Wastewater In Pharmaceutical, Chemical, Fuel Industry Esp. For Toxic Substances , Heavy Metal, Emulsified Organic Matter Excellent Removal Efficiency.
Flow Diagram
Main Technical Parameter
Model |
Volume(M3) |
Dimension(M) |
Voltage(V) |
Currency(mA) |
Power(KW) |
Tank |
Pole plate |
LEC-01 |
1 |
1.5*1.0*1.5 |
<36 |
<10 |
3 |
Steel |
Titanium Aluminum Nickel Iron Graphite composite |
LEC-03 |
3 |
1.8*1.2*1.5 |
6 |
Steel |
|||
LEC-05 |
5 |
2.0*1.3*2.5 |
9 |
Steel |
|||
LEC-10 |
10 |
3.0*2.2*2.5 |
12 |
Steel |
|||
LEC-15 |
15 |
3.5*2.2*2.5 |
15 |
Steel |
|||
LEC-20 |
20 |
4.0*2.2*2.5 |
24 |
Steel |
|||
LEC-30 |
30 |
5.0*2.4*2.5 |
32 |
Steel |
|||
LEC-50 |
50 |
8.0*2.4*3.0 |
36 |
Steel |
The Above Data Only For Reference , Please Subject To Our Final Confirmation
Applicant
-High Concentration Organic Wastewater
-High Ammonia Nitrogen Wastewater
-Electroplating Wastewater (Including Heavy Metals)
- Fluorine- Containing Wastewater
-Dying and Printing (High Chroma) Wastewater Treatment
-Paper Mill Pretreament
-Shipyard Waste Water
-Oily Water Treatment
-Agriculture Breeding Waste Water
-Aquaculture Pig Farm Waste Water Pretreatment
-Electrolytic Manganese Wastewater
-Emulsified Liquid Waste Water Pretreatment
-Landfill Leachate Waste Water Disposal
-Integrated Waste Water Pretreatment
-Circuit Board Wastewater
-Rare Earth Materials Processing Waste Water
-Aquarium One Year No Changing Water Solution
Comparison Between Electroflocculation & Traditional Process
Our company has changed the thinking of traditional mode and broke the shackles of traditional water treatment processes. In the biomethaneted spent wash of mollasses base distillery treatment, the most advanced electro-separation water treatment process is used to design and treat the biomethaneted spent wash of mollasses base distillery of the plant. The process is simple, the degree of automation is high, and the equipment is centralized and integrated, which is convenient for flexible operation. Cost savings and floor space during construction.
Note: We compare the traditional process with our process as follows:
Traditional Process |
Electro flocculation process |
Higher investment cost, Large footprint large scale of civil works with higher cost of civil construction investment Waste the company's limited space resources. The equipment requires wastewater to be treated separately. |
Low investment cost; 1/5 of traditional craft land occupation, which reduces large-scale civil construction cost and It can be treated together with a variety of wastewaters. |
No change, no modification or other use once complete the system |
The equipment is intensively integrated and can be relocated or adjusted at any time. |
High treated cost under dosing large quantity of chemicals |
Only adjusting PH value by use half or more less of chemical compared to traditional one |
Treatment effect 1. The outlet water quality is unstable, and the effluent water quality fluctuates greatly. After the dosing, the COD increased significantly in general. and the salt content in the water increases. It is not conducive to the recycling and utilization of water in the subsequent process. 2.the removal rate of textiles is ordinary ok, and the water quality tends to be unstable with the amount of the chemical dosing 3. by removing the textile fiber, but adding other substances. Such as COD sulfates. |
Treatment effect 1. The outlet water quality is stable. The treated COD will be lower than the raw water. The salt content in the effluent water is reduced. Conducive to the subsequent process of recycling and reuse of water. 2, the textile removal rate is very high, generally greater than 95-99%, and the effluent water quality is relatively stable. 3, the textile is removed, and other substances are effectively removed. Such as COD, color, phosphide etc. |
Traditional processes require shunting of different biomethaneted spent wash of mollasses base distillerys. For example; copper, nickel, zinc, aluminum should be built with several different water treatment systems. |
The electroflocculation process can complete the integrated treatment of different wastewaters. |
The amount of sludge is large due to add more chemicals |
There is no need to add chemicals, just the amount of sludge formed by the original substances in the water. The amount of sludge is 1/4 of the traditional process |
Have a strict requirements for raw water due to its poor bearing of impact energy |
Have a wide adaptability of raw water due to its strong bearing of impact energy. It can be start and stop freely. |
The system is less flexible and not suitable for moving with complicated operation difficult maintenance. |
The modular design of the system allows for a high degree of automation for any relocation. Easy to operate and to repair. |
It has a great influence on the subsequent process; UF and RO membrane cleaning are frequent, usually one or two weeks, sometimes even one day. The water outlet quality is relatively poor and the electric conductance is higher. |
Great improvements have been made to subsequent process operations. The UF and RO membrane cleaning cycle is 3-4 months. The water outlet quality is good and the conductivity is low. |
Equipment Operating Cost
Electricity Consumption: 0.1-1.5kWh/ ton As per Different Waste Water
Electrode Plate Loss: USDS 0.0014-0.0043 / M3 Water.
Electric Flocculation Operation Cost: USDS 0.0086-0.1122/M3 Water. (Electricity Price Calculated as USDS 0.072 / kW)
Installation Method
The Electrocoagulation Machine can be installed at the location near the treatment site, and the power control cabinet should be placed in the drying equipment room. If there are special explosion-proof requirements, it needs to be explained in advance.
Method of Operation
The Electrofluculation Machine is a continuous automatic operation mode, and no special care is required. The water inlet is provided with a flow meter, and the flow rate can be controlled by the valve. The water is pressurized by the pump into other processing systems, or directly discharged, and the equipment discharge can be set to manual or automatic control according to requirements.
Precautions
1.When the Electrofluculation System is not in use, It cannot be energized to avoid danger and equipment damage.
2.Do not arbitrarily power off when the equipment is working through water.
3.Do not touch the voltage output when powering up to avoid danger.
4.Keep the heat sink well ventilated when the device is powered.
5.The electrical parts must not be watered or wrapped in plastic cloth or likewise.
6.The Electrocoagulation equipment must be shut down before servicing.
7. If the subsequent process or equipment has been fouled, the treated process or equipment should be drained once every 2 hours, no less than 3 minutes each time; and the dirt should be cleaned regularly to prevent the residue from clogging the equipment and causing an accident.
8. Do not rub hard when loading or unloading equipment.
Similar Video Recommendation
You May Also Like
If you are interested in the product, contact Bossgoovideo.com for more information
- *To:
- LOREN INDUSTRY CO., LIMITED
- *Message:
-
Submit
Main Product:
Water Treatment Equipment ,
Sludge Dewatering Machine ,
Slurry or other Material Dryer ,
Integrated Sewage Treatment Plant ,
Mechanical Screen and Thickener ,
New Energy Machine or Tool