33c27662a860e978bda82a18121fe46e
9 month agoIntroduction to the main configuration of the yarn cutting section
① Two sets of adhesive grooves, made of carbon steel and treated with hard chrome plating; The thickness of the blade edge of the scraper is 1.5-3mm. The scraper blade adopts pneumatic rapid lifting, and the gap can be accurately set with an error of<0.05mm. The resin paste is evenly scraped and applied; The adhesive groove can be raised by 50mm pneumatically as a whole for easy cleaning. The bottom plate of the material trough adopts electric heating function. (Customer requests water heating)
② Two sets of liquid level gauges are installed separately for the upper and lower glue tanks to detect the liquid level inside the tank. They are linked with the online mixing and feeding system to form a closed-loop control, ensuring that the paste in the glue tank is controlled within a certain range.
③ The yarn cutting section is equipped with two sets of fiber cutting blades, which can be used simultaneously or separately. The short cut fiber length is 25.4mm/25.4mm. Each set of knife holders is equipped with a fiber dispersing device, driven by an independent motor, with adjustable speed. Used to disperse and cut fibers. Four sets of yarn blowing devices are installed at the cutting knife holder to blow the short fibers scattered on the edge of the film towards the resin paste. The blade material is SK2 material. Add static elimination device to the yarn cutting section. Configure the yarn swinging device.
④ The tension control of both the upper and lower films adopts electromagnetic brake control. At the same time, each is equipped with a set of flattening rollers. Six sets of flattening wheels are configured during the film movement to ensure the flatness of the entire process before the upper and lower films are combined. Automatic tension adjustment. (No film automatic connection function, customer requests to use hot heating bonding)
⑤ A flexible impregnation device is set up at the rear position of the film composite, using two sets of spring rollers to flexibly impregnate the fibers and resin paste by relying on the gravity of the rollers themselves.
⑥ The cutting section is equipped with a long fiber frame and a fiber woven fabric frame. This section is designed as a detachable part. The long fiber and fiber weaving device is installed in the middle position of two knife holders.
Our company produces Automatic Cutting Machine and Cutting Glass Machine also Fiber Laser Cutting Machine. Welcome to consult! |
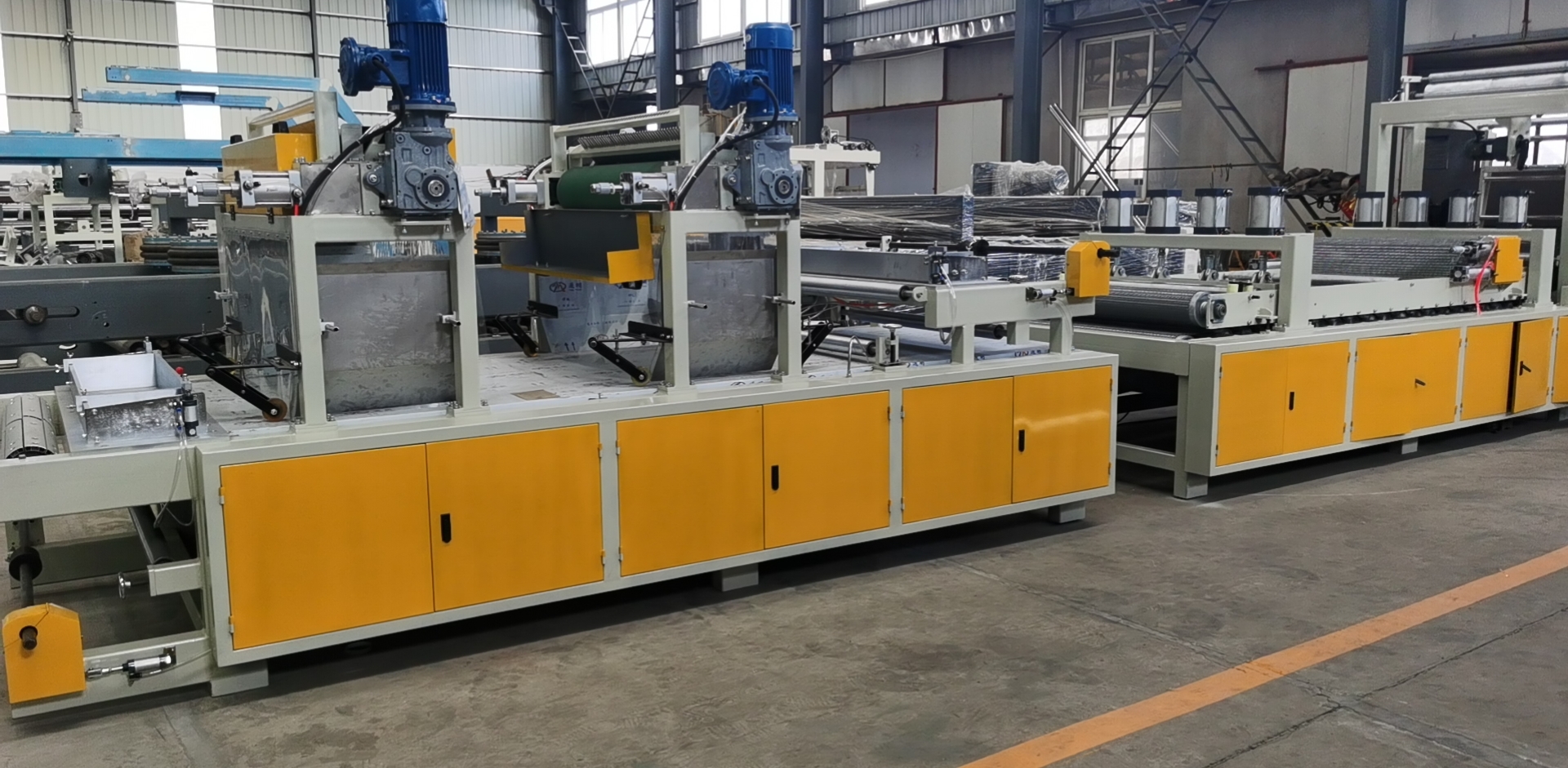
SMC sheet manufacturing equipment is a specialized device used for producing sheet molding compounds. SMC is a thermosetting plastic widely used in industries such as automotive, aerospace, construction, and electrical. Manufacturing equipment usually includes the following main parts:
1. Mixing system: used to mix resins, fillers, fibers, curing agents, pigments, and other additives uniformly in specific proportions.
2. Film coating machine: Apply the mixed material evenly onto a peelable film to form a uniform layer of plastic sheet.
3. Press: By applying pressure, the material is solidified in the mold to form the desired sheet shape and thickness.
4. Cooling system: The cured sheet needs to be cooled in a press to achieve the required physical properties.
5. Cutting and packaging equipment: Cut the cooled sheet into specified sizes and package it for transportation and storage.
The performance of SMC sheet manufacturing equipment directly affects the quality of the final product, so when selecting equipment, its accuracy, stability, and production efficiency need to be considered.
Similar Video Recommendation
You May Also Like
If you are interested in the product, contact Bossgoovideo.com for more information
- *To:
- Laizhou Parkson Machinery Technology Co., Ltd.
- *Message:
-
Submit
Main Product:
SMC Machine,
SMC Sheet Machine,
DMC Machine,
Pre-impregnating Machine,
High Speed Disperser ,
DMC Extruder
You May Also Like