black screen printing ink~1
4 month agoLow Temperature Photovoltaic PET Ink
When the photovoltaic backplane has to resist salt corrosion in the hot and humid sea breeze at 80℃, and when the PET film has to withstand ten years of ultraviolet exposure but cannot be deformed, the reflection attenuation and substrate damage of traditional solvent based ink are devouring the benefits of power stations. This Low Temperature Photovoltaic Ink redefines the performance limit of the flexible backplane with bionic optical structure and low-temperature intelligent manufacturing technology.
Three Technological Revolutions —— Hard-core Strength Penetrating the 25-year Warranty Period
Low temperature curing "light energy matrix"-unlocking 93% reflectivity at 80℃
Subversive technology:
Low temperature curing at 120-150℃ (traditional process needs more than 200℃)
The thermal shrinkage of PET substrate is less than 0.05% (the industry average is more than 0.3%).
Optical breakthrough:
The reflective layer with bionic honeycomb structure has an ultraviolet-visible light reflectivity of 92.5%.
The transmittance in infrared band is increased by 15%, and the working temperature of the module is reduced by 8-12℃
Salt spray nemesis-"titanium armor" of coastline
Extreme test data:
After 5000 hours of salt spray test (ASTM B117), the reflectance attenuation is less than 0.8%.
After soaking in 5% saline for 30 days, the adhesion retention rate was > 99%.
Self-repairing black technology:
Microencapsulated silane is automatically released in case of moisture, and microcracks below 3μm can be repaired.
Electrolytic corrosion current < 0.2 μ a/cm (IEC 62716 standard).
The King of Boiling Performance —— The "Ultimate Survivor" in Hot and Humid Environment
Double 85 strengthening test (85℃/85%RH):
After 3000 hours, the yellowing index Δ b < 1.0 (invisible to the naked eye).
Adhesion after boiling test (100℃/48h) ≥4B(ASTM D3359).
Actual combat case:
A floating power station in Southeast Asia experienced the rainy season erosion, and the annual attenuation of the backplane reflectivity was only 0.2%.
Industry 4.0 intelligent adaptation-the "invisible pusher" of mass production accuracy
▍Screen Printing Equipment Intelligent Parameter Package
Screen adaptation: Aluminum Screen Printing Squeegee with 120-200 meshes is fully supported.
Intelligent matching of scraper hardness 70-90 Shore A
0.1mm precision line printing (edge burr < 5 μ m)
Dynamic control:
Automatic viscosity compensation (800-5000cps real-time adjustment)
Curing temperature fluctuation ≤ 1.5℃ (industry 5℃)
▍ Aluminum Screen Printing Squeegee Synergy Scheme
Life multiplication technology:
Scraper wear rate decreased by 72% (thickness loss after 100,000 printing < <0.02mm).
Nano-coating reduces scratch resistance by 45%
Cost revolution:
The ink consumption per square meter is reduced by 33% (compared with traditional ink)
Screen cleaning frequency is reduced from 3 times per shift to 1 time per day.
Survival Archives in Extreme Environment —— An Empirical Study of Exceeding Standards
Polar challenge
Alaska off-grid power station (-45℃):
No peeling of coating after ice storm impact.
After 500 freeze-thaw cycles, the adhesion retention rate was 99.5%.
High Desert Kill
Sahara photovoltaic array (surface temperature 70℃):
After the sand-dust abrasion test (ISO 13321), the reflectivity keeps 91%.
The UV aging resistance reaches the highest level of IEC 61215.
Corrosive purgatory
Middle East Seawater Desalination Plant (salt spray concentration 8 mg/m):
Chloride ion permeability is less than 0.005 mg/cm day.
Backplane insulation resistance > 100g Ω (safety standard > 5g Ω)
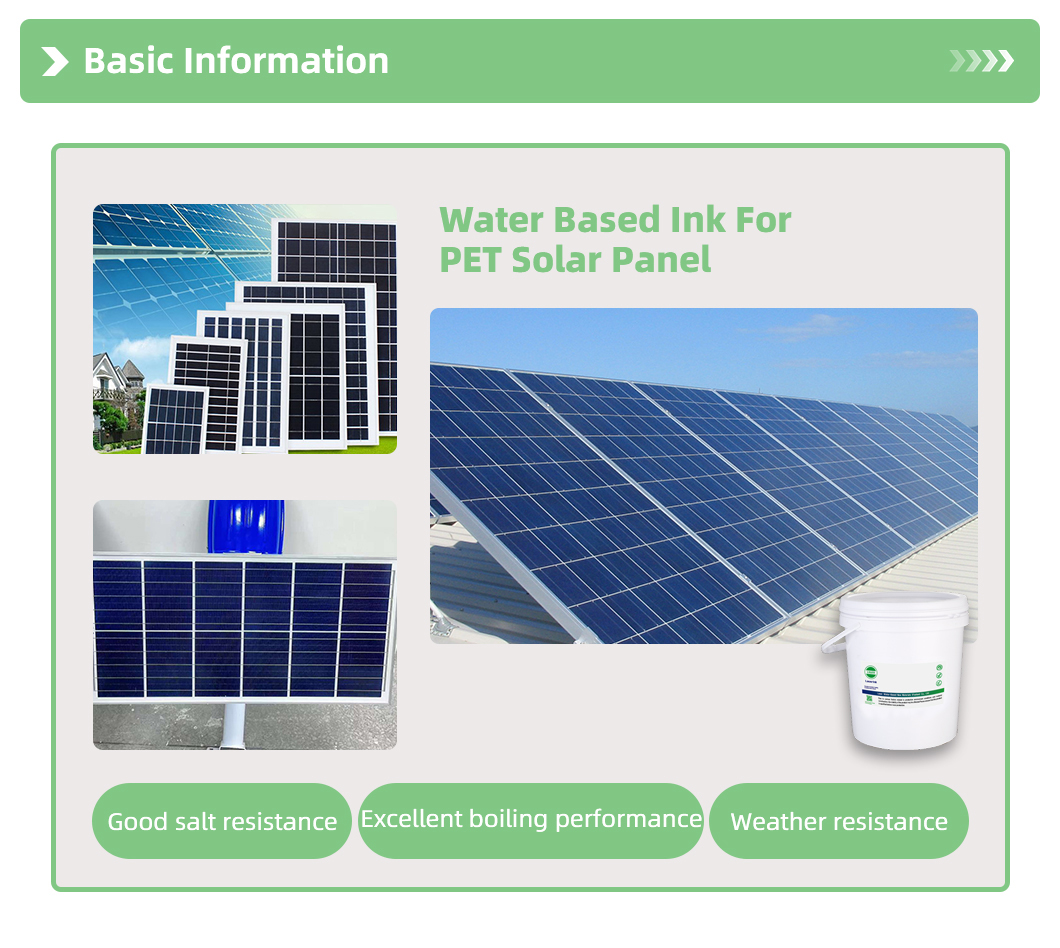
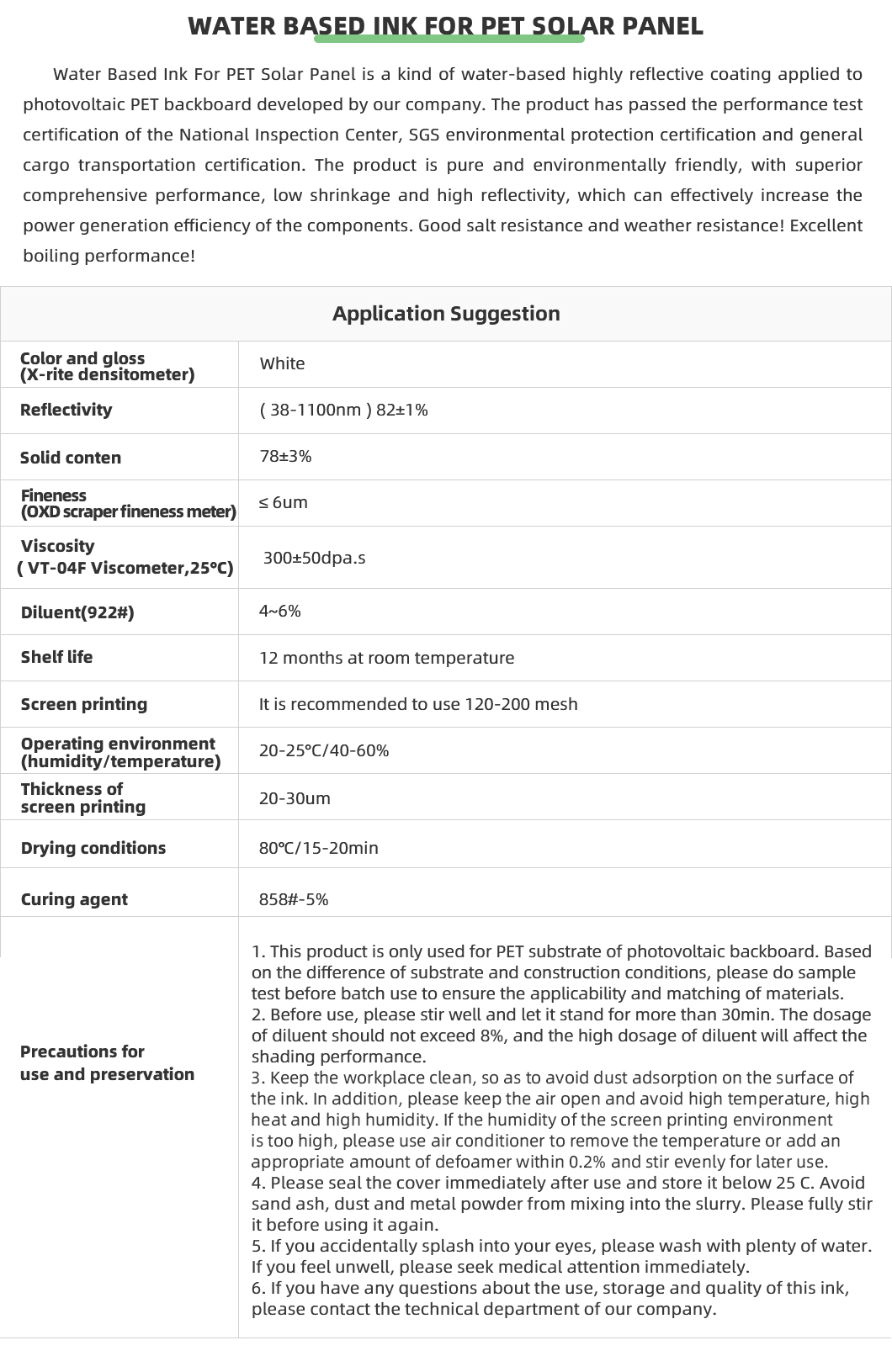
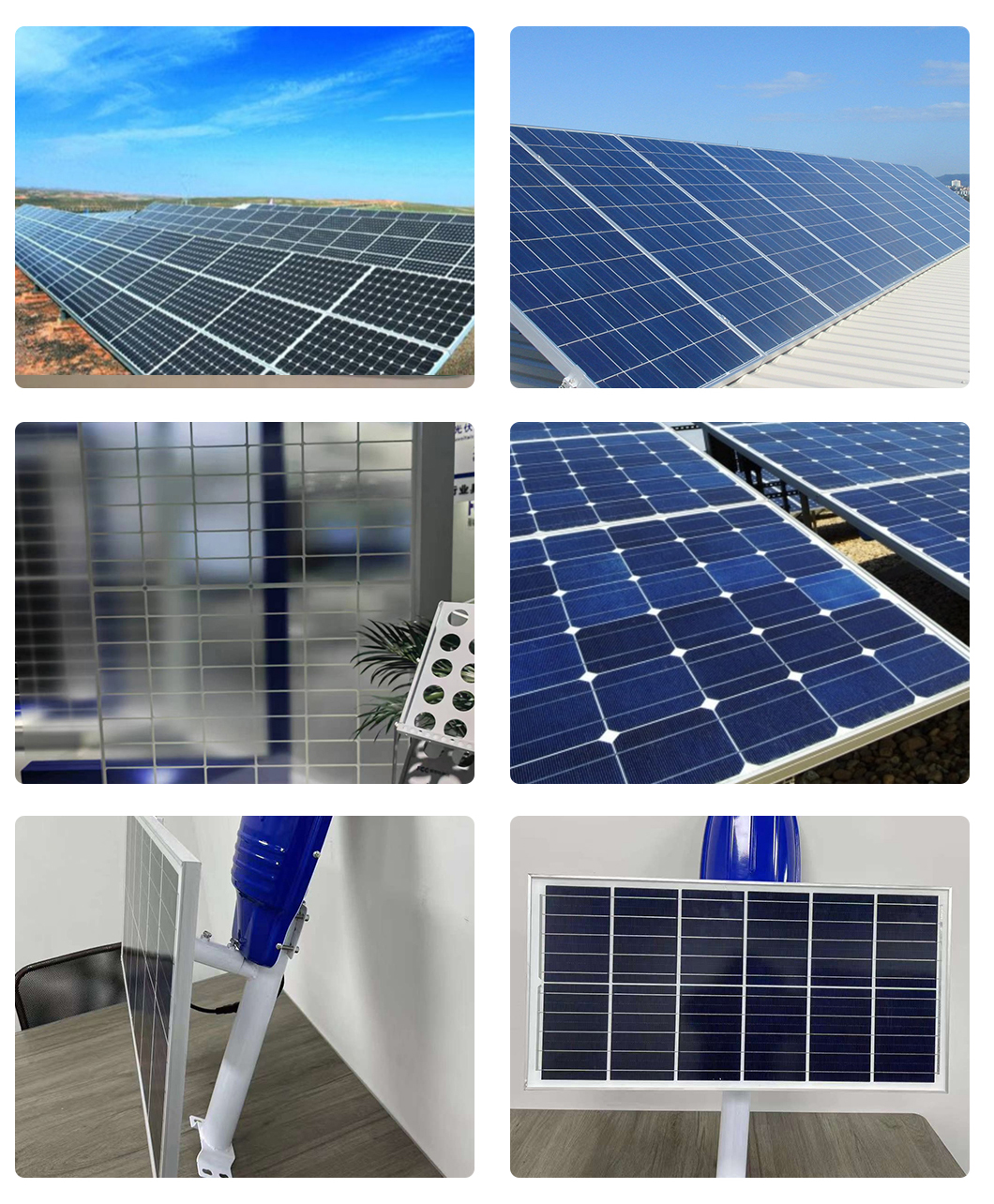
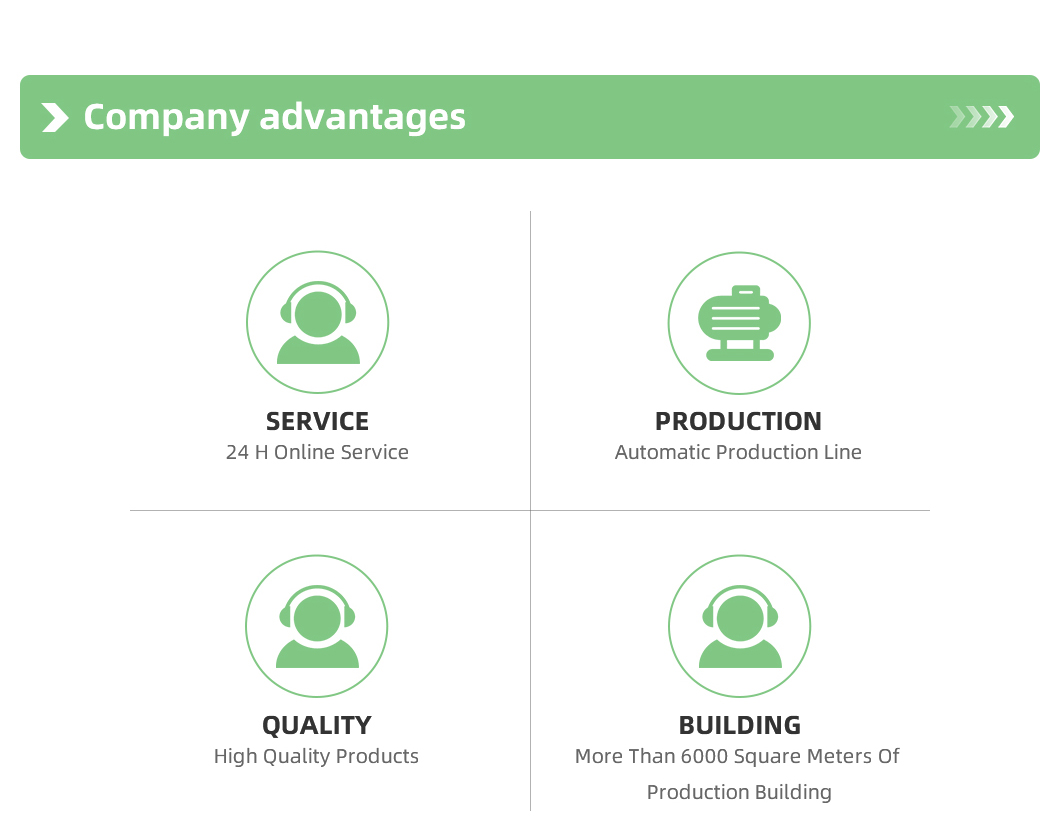
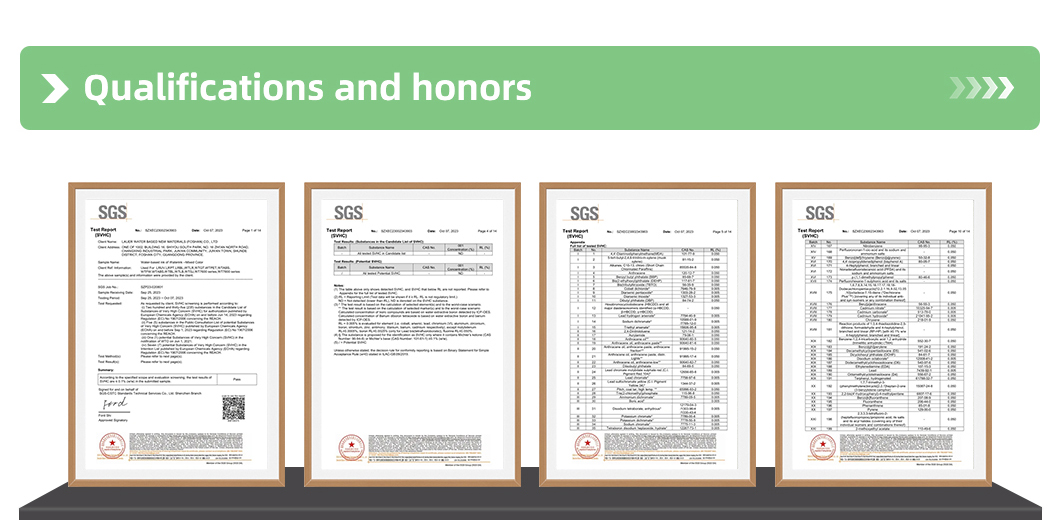
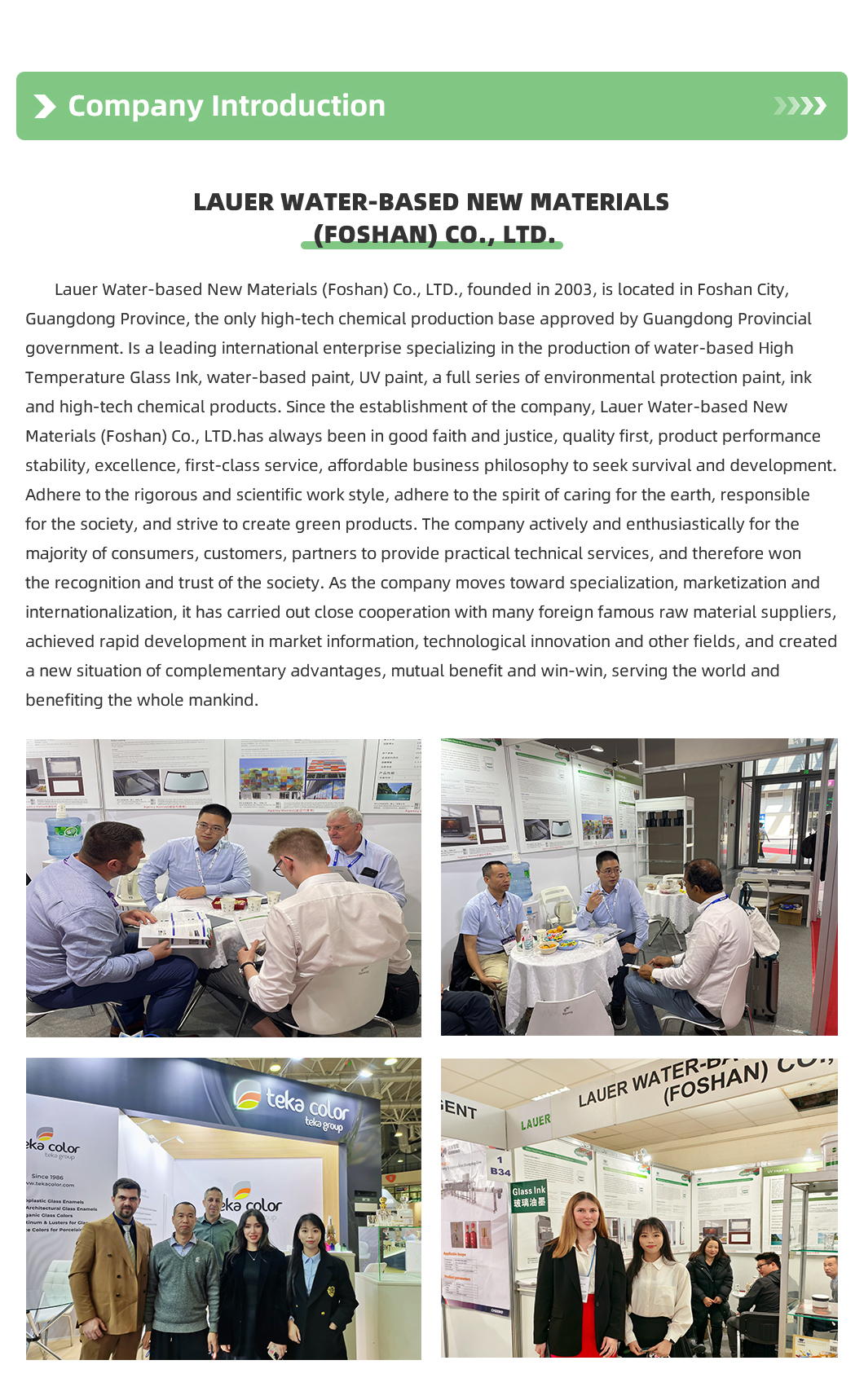
Similar Video Recommendation
You May Also Like
If you are interested in the product, contact Bossgoovideo.com for more information
- *To:
- Lauer Water-Based New Material(Foshan)Co.,Ltd.
- *Message:
-
Submit
Main Product:
Water Based Ink,
Glass Ink,
Screen Printing Ink,
UV Ink,
Printing Ink ,
Water Based Screen Printing Ink