Hydraulic plate valve
4 month agoInstallation location: It should be installed in a location that is convenient for operation and maintenance, and there should be enough space around it for maintenance, debugging and replacement of parts. At the same time, ensure that the installation environment is clean and dry to prevent the valve from corrosion, pollution and mechanical damage.
Installation direction: Generally, it should be installed according to the flow direction mark of the valve to ensure that the flow direction of the medium is consistent with the design flow direction of the valve to avoid reverse flow causing valve damage or poor sealing.
Pipeline connection: When connecting the pipeline, ensure that the axis of the pipeline coincides with the inlet and outlet axes of the valve to avoid additional stress and bending moment that affect the normal operation and sealing performance of the valve. The connecting bolts of the pipeline should be tightened evenly to prevent leakage due to uneven force.
Pre-operation inspection: Before operating the valve, the appearance, connection parts, seals, etc. of the valve must be fully inspected to ensure that the valve is not damaged, leaking, loose, or other abnormal conditions. At the same time, check whether the pressure, oil temperature, oil level, etc. of the hydraulic system are normal, and whether the hydraulic pipeline is firmly connected and leak-free.
Operation method: The operator should be familiar with the operation method and control principle of the valve and operate it strictly in accordance with the operating procedures. Generally speaking, the valve is opened and closed by controlling the pressure and flow of the hydraulic system. During the operation, pay attention to the movement of the valve to ensure that the valve is opened and closed smoothly and quickly to avoid stuck, impact and other phenomena.
Opening and closing speed: The opening and closing speed of the valve should not be too fast or too slow. Too fast may cause sudden changes in the pressure of the hydraulic system, water hammer, and damage to the valve and pipeline; too slow may affect production efficiency and even cause medium leakage. The opening and closing speed of the valve should be reasonably adjusted according to the specific working conditions and
Avoid misoperation: During the operation, avoid misoperation, such as mispressing the control button and misadjusting the hydraulic system parameters. At the same time, set obvious operation signs and warning signs to prevent misoperation by unrelated personnel.
Regular maintenance: Regularly maintain the valve, including cleaning the outside of the valve, checking the wear of the seal, replenishing or replacing the hydraulic oil, checking the filter of the hydraulic system, etc. It is generally recommended to perform a comprehensive maintenance every certain period of time or after a certain number of operations to ensure the performance and reliability of the valve.
Seal maintenance: Seals are key components to ensure the sealing performance of valves. Seals should be checked regularly for wear. If seals are found to be aging, deformed, or severely worn, they should be replaced in time. When replacing seals, seals of qualified quality and matching specifications should be selected and installed in the correct way.
Hydraulic system maintenance: Regularly maintain the hydraulic system, including checking the working conditions of hydraulic pumps, hydraulic cylinders, hydraulic valves and other components, cleaning or replacing the filters of the hydraulic system, and checking the quality and oil level of the hydraulic oil. If abnormal conditions such as leakage, unstable pressure, and excessive oil temperature are found in the hydraulic system, they should be repaired and handled in time.
Pressure safety: During use, ensure that the pressure of the hydraulic system does not exceed the rated pressure of the valve to avoid damage or leakage of the valve due to excessive pressure. At the same time, reasonable pressure protection devices, such as safety valves and overflow valves, should be set up. When the system pressure exceeds the set value, the pressure can be relieved in time to protect the safety of valves and equipment.
Prevent leakage: The valve may leak during use, and leakage problems should be discovered and handled in time. If the leaked medium is toxic, harmful, flammable, explosive or other dangerous substances, appropriate protective measures should be taken, such as wearing protective equipment, setting up leakage alarm devices, etc., to prevent accidents.
Personnel safety: When operating and maintaining valves, operators should wear necessary personal protective equipment, such as safety helmets, safety shoes, gloves, etc. At the same time, care should be taken to prevent the high-pressure oil of the hydraulic system from splashing and injuring people. When performing inspection and maintenance work, the power supply of the hydraulic system should be cut off first, and appropriate safety measures should be taken, such as locking valves, hanging warning signs, etc.
If you need, please contact us.
Product name | Self-locking hydraulic flat valve |
Specification model | 3 1/8 |
Implementation standard | API 6A |
Rated working pressure | 15000psi |
Product specification level | PSL1~PSL3G |
Product performance level | PR1~PR2 |
Temperature level | PU, LU |
Material level | AA~FF |
Product color | green |
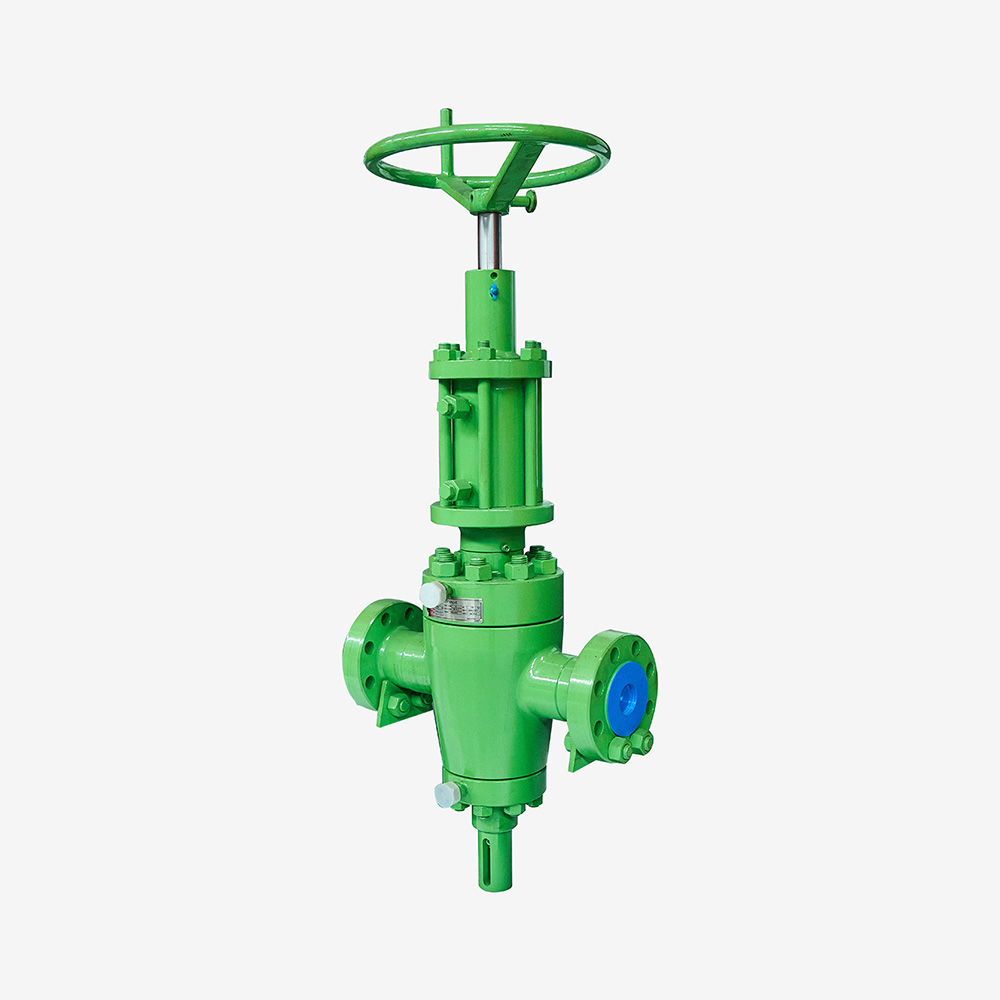
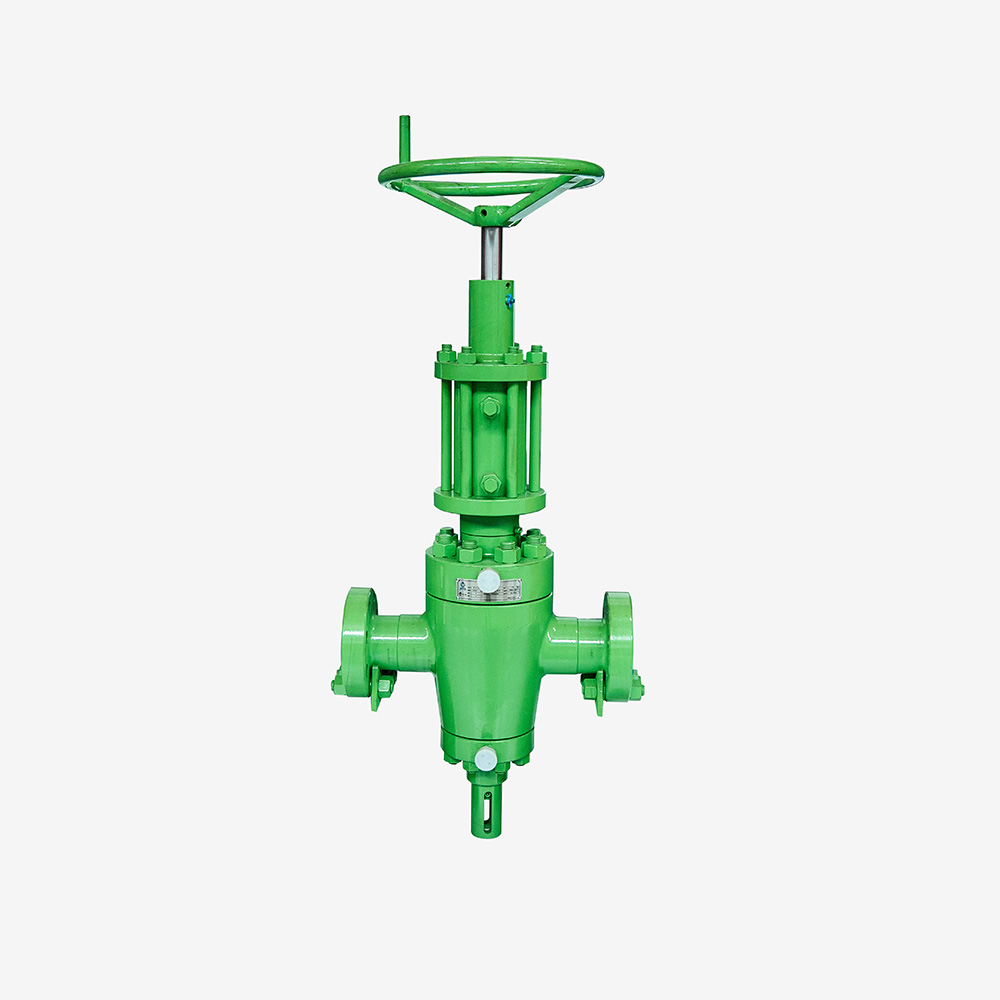
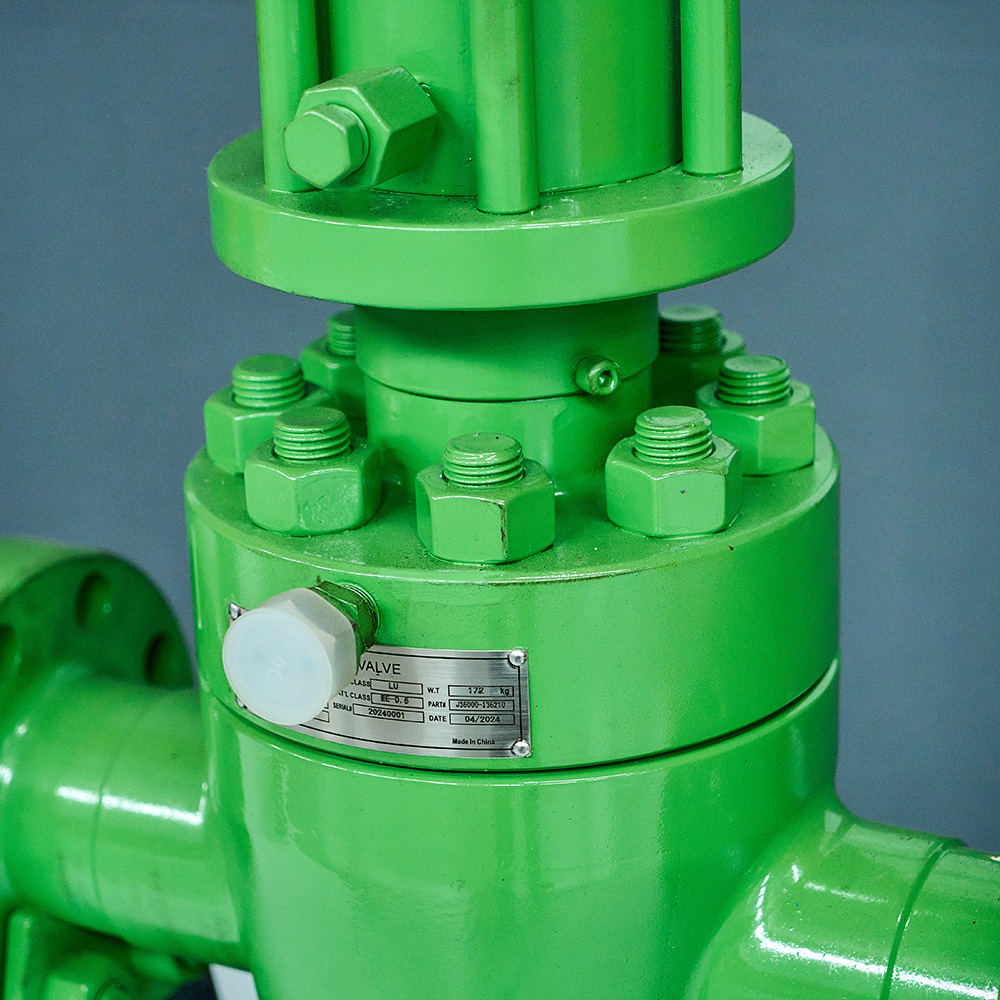
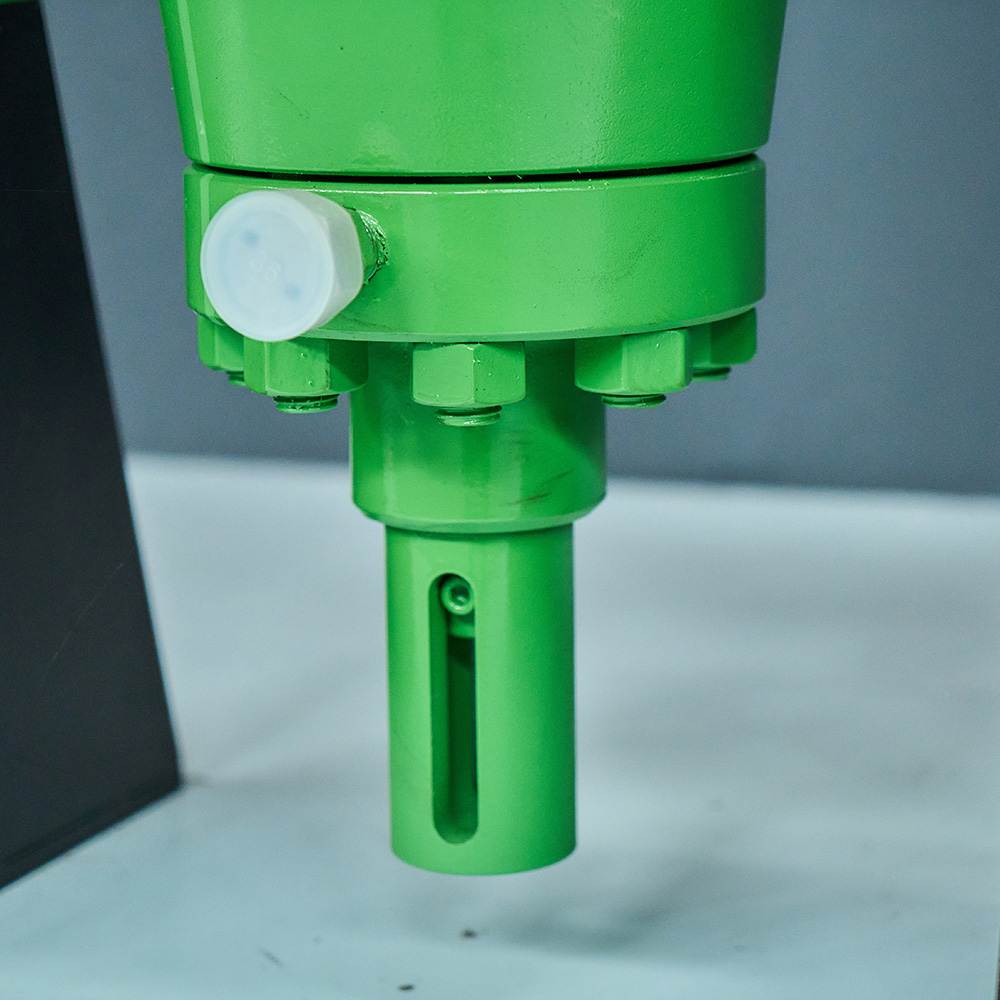

Similar Video Recommendation
You May Also Like
If you are interested in the product, contact Bossgoovideo.com for more information
- *To:
- Jianhu Fulida Machinery Manufacturing Co. , Ltd.
- *Message:
-
Submit
Main Product:
Oilfield wellhead device,
Drilling and production equipment valve,
Blowout preventer,
Fracturing Manifold,
Forged steel flange ,
Forged parts of wellhead manifold
You May Also Like